Case Study PESA
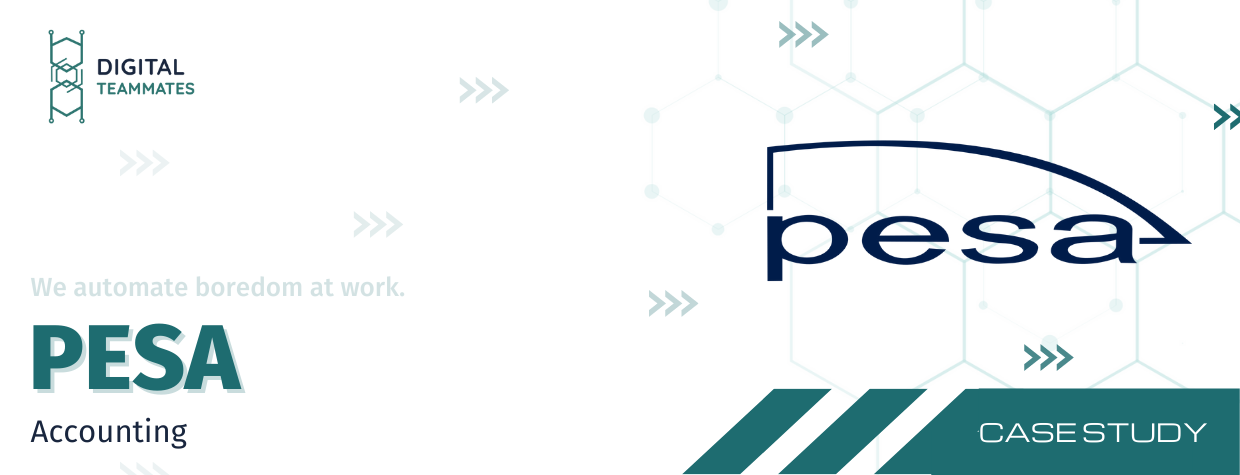
PESA S.A. is the largest Polish manufacturer of rail vehicles. It also deals with modernization, repair, and inspection of rolling stock. The company employs several thousand people in many locations in Poland. As they emphasize, the mission and ambition of all employees are to supply high-quality products and satisfy both customers and users. They cooperate with leading scientific and research centres, but their strength is primarily a highly qualified and experienced team that has decided to cooperate with Digital Teammates.
Departure station – how it all started?
The idea to implement RPA (Robotic Process Automation) in PESA appeared in quite unusual circumstances. It all started with the accounting department, where they had noticed that a large part of the team would have started the retirement process soon. So, the company decided to seize the moment and automate processes instead of starting an expensive recruitment cycle.
PESA constantly looks for new ways to facilitate repetitive work, so has been inevitable to look for an appropriate solution in new technologies used in the fintech industry.
What were the conditions for this process improvement?
According to the company, such a change should be:
- profitable,
- relieving employees from tedious tasks,
- allowing to handle all requests flawlessly.
Initially, PESA tried to deploy OCR (Optical Character Recognition) combined with Excel macros. However, it quickly turned out that the best solution would be to employ Digital Teammates. The robots helped not only with the upcoming rotation, but also allowed PESA to deal with the tedious processing of statements, invoices, and delegations.
PESA and Digital Teammates on the same track
The most common challenge at the beginning of almost any cooperation is learning how to communicate. PESA employees attempted to learn how robots work. On the other hand, we tried to get to know the specifics of PESA’s work and observe the behaviour patterns of people employed in PESA in detail. It all started with the process related to bank statements and MT940 files. Over two job positions were involved in the processing of the statements, and the number of monthly tasks was counted in thousands. The large spikes in the MT940’s file volumes showed enormous robotic potential. As you know, such large companies as PESA cannot afford to stand still, which is why financial and accounting processes in PESA have been automated in the first place. The tasks of robots at that time included: checking accounts and verification of positions on the so-called “whitelist”. The next step in automation was invoice processing. There were registering around 20,000 invoices per month. Thanks to our solutions, the invoice box has been properly adapted to the needs of the company. We can even say that Digital Teammates has received its email. In total, thanks to excellent communication, it was possible to automate more than 17 processes, which concerned not only statements and invoices but also business trips and even the factoring process.
Terminal station… but are you sure?
The cooperation between the companies turned out to be fruitful. PESA employees learned how to create very detailed instructions for systems and task instructions for robots while we got to know ins and outs of PESA’s work. Thanks to this, the implementation of RPA solutions was smooth and effective. However, it is worth remembering that automating a few processes does not mean the end of cooperation. We are still identifying new areas with robotic potential, but we are also constantly updating our robots. Weekly, it is up to 11 updates to ensure that Digital Teammates are fully operational.