Can everyone develop software robots?
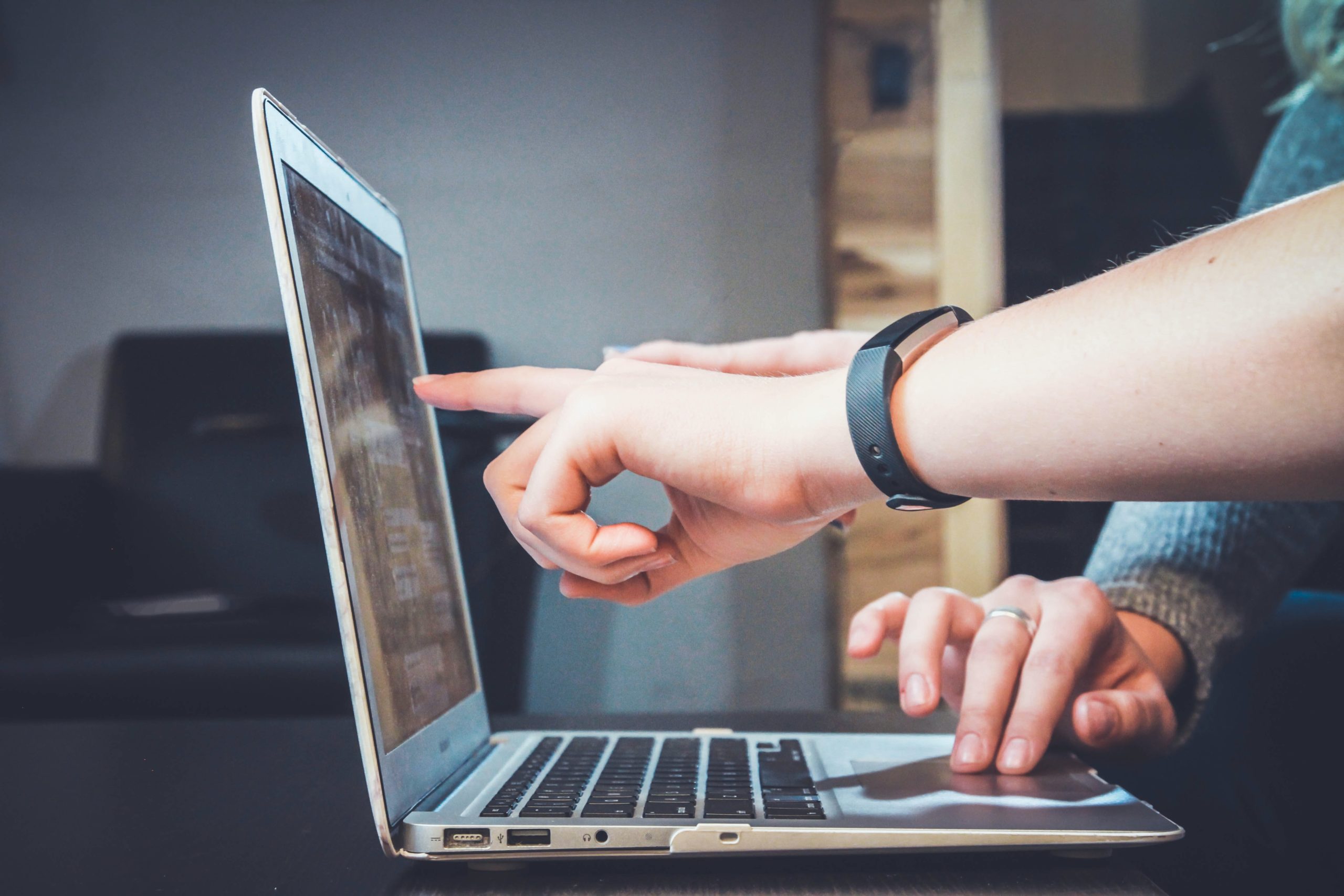
TL; DR
Democratization of the software robot development process will be successful if we take care of 3 things:
- green light from decision-makers;
- employee engagement;
- high-quality engineering process.
Contrary to appearances, the most difficult thing is to meet the third condition, which does not mean that the first two are easy to accomplish. In the article, you will find practical tips on how to reach these conditions.
IDC and UiPath report
In December 2020, IDC, together with UiPath, published a report: “A Robot for Every Worker: Are We Ready for a People-First Automation Mindset?”.
Based on surveys conducted among 431 companies from 19 industries employing at least 250 employees, the authors analysed the potential of the so-called democratization of the robot development process. They involved the widest possible group of employees actively working on robotization. The target state would be the title – Robot for each employee. Now, this is difficult to achieve due to the limited resources that can be spent on building and maintaining robots.
Is robot development a job for everyone?
The report shows the distance between us and this goal. It turns out that 80% of decision-makers in companies that use robotization give employees access to RPA tools. In this group, 22% of respondents rate the program as a great success and 71% as a moderate success. At first glance, these numbers do not look too bad, but it turns out that only 11% of employees have created robots that have ever entered production use. The workers themselves are also not overly enthusiastic – 25% expressed a strong desire to participate in the robot building program. Another 38% said they might have participated, and another 27% refused to participate.
These data clearly show that the road to democratization is still long. This is certainly partly the result of decision-makers attitude to its idea. As many as 53% of those who actively support the idea have a negative opinion about the value of a robot for each employee (and as many as 79% of those who do not support democratization).
In addition, these robots lack clear business value. It’s hard to imagine that every employee is doing enough repetitive and frustrating tasks to be profitable to be robotized and maintained.
A new approach to robotization.
Hence, the authors of the report propose to depart from the classic Process First approach, which focuses on improving its efficiency, quality, speed, and reducing costs. The new goal would be to take care of employees (People First). Due to the simple observation that employees who feel valued and enjoy their job perform better at doing their tasks. It results in lower operating costs – lower turnover and reduced costs of training new people.
The authors of the report are full of optimism about the idea of democratization, giving ideas on how to implement it. If you are interested, I encourage you to read the entire study.
On the other hand, I would like to ask whether the care for employees should be expressed through the democratization of the robot production process? Especially that, according to the survey, the employees and decision-makers themselves treat this idea with reserve.
How to deal with decision makers?
It is difficult to successfully implement any initiative without the support or even neutrality of decision-makers. The surveys show that most of them, even if they understand the non-financial benefits of democratization, are not convinced that it brings value to the company. From my point of view, this challenge can be overcome by selecting processes that have clear and measurable benefits at the same time. These do not necessarily have to be financial benefits, although such benefits most easily appeal to the imagination of decision-makers. You may as well rely on tangible performance or quality indicators.
In most cases, increasing the efficiency or reducing the number of errors in the process can ultimately be translated into real money. By showing that it is possible to achieve the objectives of Process First and People, it will be easier to convince decision-makers that the initiative of democratization makes sense. Over time, having more employees trained in automation, we can reach for processes with a weaker business case. Thanks to more and more experience, subsequent implementations should be cheaper, less error-prone, and shorter.
How to engage employees in automation?
The authors of the report devote a lot of space to persuading employees to engage in automation activities. In my experience, this task is even more difficult than convincing decision-makers. Building robots sounds very attractive and gives great satisfaction but is still associated with a difficult engineering process. Therefore, most people rate their ability to master robotic platforms very low. Certainly, the providers of Low-Code platforms or even No-Code have done a lot to make it more intuitive. Coding support tools and even robot recorders are available. Unfortunately, achieving proficiency still requires a lot of time, especially when you need to go beyond the scheme established with the help of ready-made components.
The natural fear of programming is also a big challenge. When the final robot has access to sensitive data or financial data. It is often the case that we have limited access to testing environments in which it is safe to experiment with robot manufacturing. Then such fears are well-founded.
The answer to these challenges should be to create the best possible conditions for a smooth entry into robotization. We do not have to require full involvement in the entire development cycle from the very beginning. For starters, it is helpful for employees to understand how to find robotic potential in everyday tasks. Not only in terms of their feasibility to automate, but also economic criteria or overcoming technical barriers. In this way, ideas for robots have a greater chance of being implemented, and thus employees are more motivated to search further.
A separate activity that does not require technical skills is testing robots and then submitting extensions for their functionality. It can also be a task gradually familiarizing you with technical terminology and allowing you to influence the final shape of the robots.
A good opportunity to gently enter the world of robotization is hackathons, workshops, or online training, in which you can take part. They will help to check if we feel good as a full-fledged robot creator.
In my experience, we will always find people who would like to join the Robotic Competence Center with commitment. Others will find new skills that they want to develop in parallel with their daily duties. However, everyone, without exception, will gain knowledge that will facilitate the search for potential and the implementation of robots in the future. And this will lower the costs of projects and allow you to reach for tasks with a lower robotic potential. Such tasks in the regular capacity assessment process would never have a chance of being launched.
In this case, is the conviction of decision-makers and employees’ commitment a guarantee of the success of the robot idea for everyone?
Is it more about people or technology?
It turns out that there is one more difficulty that must be overcome at the very beginning. Even if we use modern tools that require minimal technical knowledge, the robots will ultimately remain software that undergoes the normal engineering process. In this process, the coding is usually a small slice of the whole. There is no place here to describe all its elements, but you should think about:
- Proper code versioning,
- Automated code migration between environments,
- Automated robot testing,
- Developing best practices and benchmarks.
Usually, these sub-processes are handled by engineers who have the skills and knowledge of the whole, so they can cope even in exceptional situations. In addition, each software development process should assume minimal outlays for subsequent maintenance, which can be achieved by high standardization of development. It is not easy to require this from people who are inexperienced or perform programming tasks as an extra occupation.
There is a need for a highly mature Robotic Competence Center in the organization, based entirely or mostly on automated robot manufacturing processes, to enable it to be extended to employees from business units. Good practice in this situation is, first, to reach this maturity before we start the process of democratization. If the robot factory works flawlessly, you can start expanding it with more people, while keeping an eye on the metrics, especially related to the quality of the software. It should also be remembered that the final responsibility, control, and monitoring of both the development and maintenance of robots should remain with the Robotics Competence Center.
Summary
Summing up, the idea of democratizing the development of robots is worth attention and recommendation, but still difficult to apply in practice, especially on a large scale. Wherever we have the ambition to employ dozens, hundreds, or even thousands of employees in the engineering process for the company, we must first take care of:
- Proper coordination of their activities,
- Appropriate level of competence,
as well as give satisfaction with the results of their work and outline the prospect of long-term development. All these aspects are not only critical to the success of the project but also complex and overly ambitious.
Certainly, democratization is the next stage of maturity for companies that strategically think about automating their processes not only in the context of greater efficiency but also in increasing employee engagement.
The IDC and UIPath reports show the path to achieving this goal. I will be curious to follow the successive stories of the organizations that managed to achieve it.